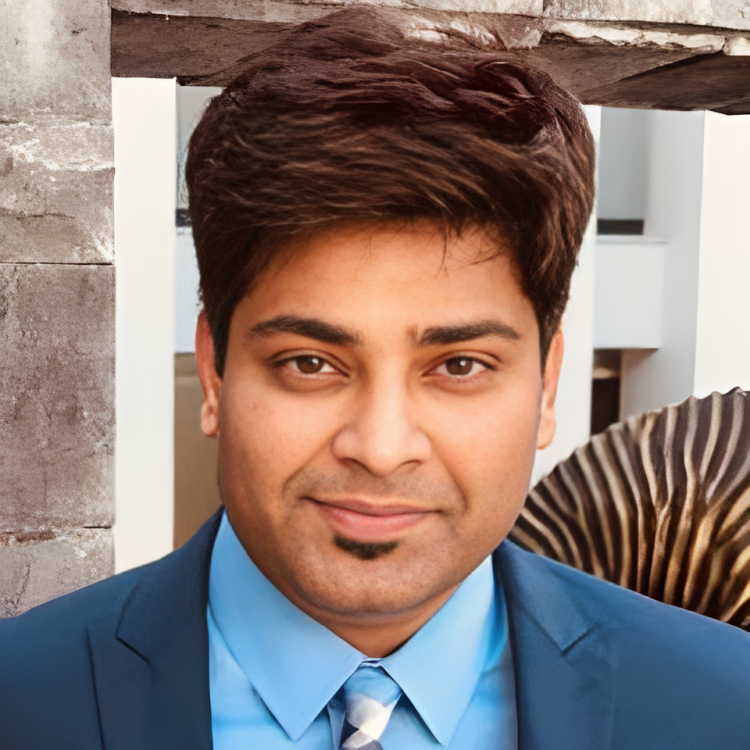
More and more, the key to success in industrial facilities or process plants often lies in mastering the art of digital transformation. In the realm of maintenance operations, this transformation comes in the form of work order digitization. Traditional, manual work order processes are fraught with challenges that can hinder efficiency and productivity. In this blog, we will delve into the pain points associated with legacy work order processes and explore how transitioning to a digital system using mobile devices can deliver a host of benefits.
The Pain Points of Legacy Work Order Processes
According to Sundeep V. Ravande, the CEO of Innovapptive, Inc., here are the pain points of legacy work order processes:
No Real-Time Visibility: One of the most significant drawbacks of traditional work order processes is the lack of real-time visibility. Maintenance teams often struggle to monitor the status of ongoing operations, leaving them in the dark about asset conditions and performance.
Poor Resource Allocation: Without real-time data, resource allocation becomes a guessing game. Maintenance teams may deploy technicians inefficiently, leading to wasted time and resources.
Change Management: Adapting to changing maintenance requirements can be a cumbersome process in manual systems. Updates and adjustments often entail a tedious and time-consuming process.
Slow Response Times: Manual work order processes are notorious for their slow response times. This lag can prove costly, especially in situations that demand swift action.
Lack of Tracking Capability: Tracking asset performance and maintenance history becomes an uphill battle in legacy systems, making it challenging to make data-driven decisions.
Data Gathering and Sharing: Gathering and sharing critical maintenance data is often a manual, error-prone process. This not only slows down operations but also increases the risk of data inaccuracies.
Not Well-Suited for Emergencies: In emergency situations, traditional work order processes can prove to be insufficient and ineffective. Quick decision-making and action are crucial during crises.
Communication Delays: Effective communication is the lifeblood of maintenance operations. In manual systems, communication often suffers from delays and misinterpretation.
Manual Entry into ERP: Integrating maintenance data into an Enterprise Resource Planning (ERP) system involves manual data entry, which is not only time-consuming but also prone to errors.
The Transformation: Going Digital with Mobile Devices
Ravande goes on to explore the transformative benefits of digitizing work order processes through mobile devices:
Real-Time Visibility: Digital work order systems offer real-time visibility into maintenance operations, regardless of an asset's geographical location. Maintenance teams can monitor asset conditions, progress, and performance at their fingertips.
Internet Independence: Unlike traditional systems that may rely heavily on internet connectivity, mobile devices equipped with offline capabilities ensure that maintenance tasks can continue even in areas with limited or no internet access.
User-Friendly Interface: Digital work order systems boast user-friendly interfaces accessible to a diverse workforce, from shop floor technicians to C-suite executives. This inclusivity promotes ease of use and adoption.
Paperless Workflows: Going digital means saying goodbye to paper-based processes. Employees can carry out tasks with a mobile device in hand, reducing the need for physical paperwork and promoting mobility.
Proactive Maintenance: With the ability to track equipment performance, digital systems provide key data before costly breakdowns occur. This shift from reactive to proactive maintenance can save time and resources.
Equipment Location Tracking: Tracking equipment location digitally can expedite maintenance work order fulfillment, ensuring that resources are allocated efficiently.
Safety Compliance Notifications: Digital systems can automatically notify relevant personnel when equipment operates beyond safety compliance thresholds, enhancing workplace safety.
Automated Work Order Generation: Digital systems enable the automatic generation and tracking of work orders, eliminating the need for manual data entry and reducing the risk of errors.
Operational Transparency: Perhaps one of the most significant benefits of digitization is the increased operational transparency it offers. Decision-makers have access to real-time data, allowing for informed choices and streamlined operations.
The journey from legacy work order processes to digital mastery is marked by a profound transformation in maintenance operations. The shift to mobile device-driven digitization addresses the pain points of traditional systems and delivers a host of benefits, including real-time visibility, user-friendliness, proactive maintenance, and operational transparency. In an era where adaptability and efficiency are paramount, embracing work order digitization is a step in the right direction for organizations aiming to stay ahead of the curve.
Join the Conversation