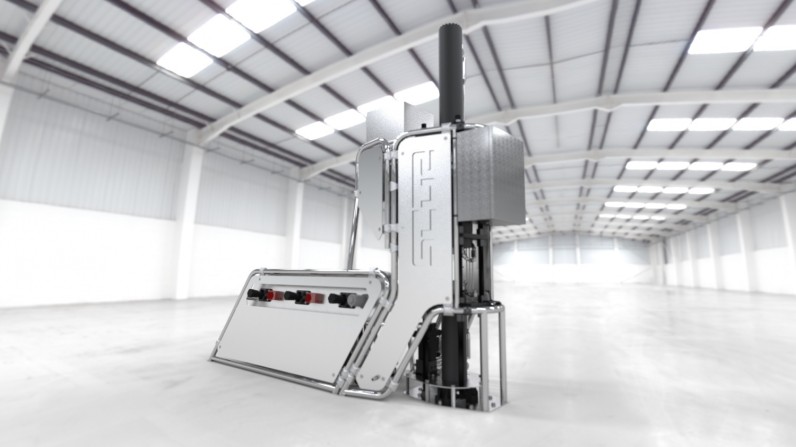
Traditional waste management practices in the food processing industry significantly impact the environment, producing substantial wastewater, solid waste, and greenhouse gas emissions. Moreover, these methods are often inefficient, leading to increased operational costs and reduced profitability. The expense of waste disposal is considerable, and frequently, the potential value of waste materials remains untapped.
Fortunately, SCO2, Inc. has developed an innovative solution that not only cuts down on waste but taps into its potential. Under the guidance of Co-Founder Olaf N. Lee and CEO Michael Sigel, SCO2 is leveraging advanced supercritical CO2 separation technology to revolutionize industrial-scale waste management in the food processing sector. Their innovative approach not only addresses environmental concerns caused by food processing but also unlocks new significant revenue and profits.
Sigel explains, "The big issue is processors think they have a 'disposal' problem vs a 'high value' opportunity. As a former food processor, I understand that dilemma. When you have what you perceive as waste, it is hard to see it as anything but a problem. As a result, the landfill becomes the easy option—even though it carries a true financial and environmental cost. Companies don't realize they're literally throwing away a revenue opportunity."
Processors fundamentally do not have an efficient, cost-effective, scalable way to convert their waste into high-value ingredients, flavors, or other bioactive compounds. SCO2 is at the forefront of addressing this challenge with breakthrough improvements to Traditional Supercritical CO2 technology. This extraction method has been around for 50+ years and is a proven, green extraction solution that is effective at extracting high-value compounds. However, these systems are complex and costly to operate, preventing them from being used for industrial solutions.
Sigel adds: "Traditional systems are saddled with multiple manual steps from grinding, bagging, loading and unloading material and complex downstream separation steps—adding more time, specialized equipment and skilled labor which add significant costs. SCO2 has eliminated most of these steps and patented a simple, automated solution that scales cost-effectively."
Founder Olaf Lee's background in the waste processing industry drove the essential design requirements for SCO2's industrial solution, which is capable of processing 5–50 tons of material per hour. "The key for industrial equipment is reliability and maximizing uptime. To do that, you design a simple system with proven, widely available parts you can depend on. Our clients have enough headaches. Their expectation is that SCO2 Technology will be a consistent, cost-effective, hassle-free workhorse helping them unlock significant revenue & profit."
"Parts of our food system are broken. We waste nearly 33% of what we produce, and we can do better. The trick is deploying scalable solutions that drive adoption. In five years, SCO2 technology can help reduce food waste by 100 million tons per year. That moves the needle," Sigel asserts. "We are showing our clients that being sustainable and being profitable are not mutually exclusive. They can both be true at the same time with SCO2."
Scaling SCO2's operations to meet the growing demand will require strategic partnerships and additional capital investment, but with SCO2 positioned for substantial growth, potentially reaching a billion-dollar market valuation, they feel good about where they stand. Sigel emphasizes, "The trajectory towards broader adoption of SCO2 technology not only promises a greener, more sustainable future for the food processing industry but a profitable one as well."
To learn how you can get involved in SCO2's mission, go to sco2.net.
Join the Conversation